The hydraulic cutout disables the boom movements when the machine is lifting a load
greater than the capacity for that region.
The following sections serve to illustrate common electrical connections from the Gen 3 safety system to the existing electronics in the machine. The purpose of this Tech Doc is not to provide a wiring setup for any specific telehandler, but rather to provide generic guidance for customers when trying to troubleshoot electrical cutout issues.
There is usually a hydraulic cutout function in use with the existing Longitudinal Moment
Indicator (LMI). Typically this cutout stops the boom lower and extend functions while
leaving the raise and retract functions still operable - this is called an aggravated movement
cutout. An aggravated movement cutout can be used with the Gen3 LMS. Ideally the
cutout produced from the LMI should be connected in series with the cutout produced by
the Gen3 LMS, so if either system go over capacity they can produce a cutout. A 6-Pin connector with 6 bare wires will have been supplied with the kit - called the machine
cutout connector. This connects to two relays in the CCIM module according to the table
below. The relays are capable of switching up to 5 A of current, so can directly drive
solenoids if required.
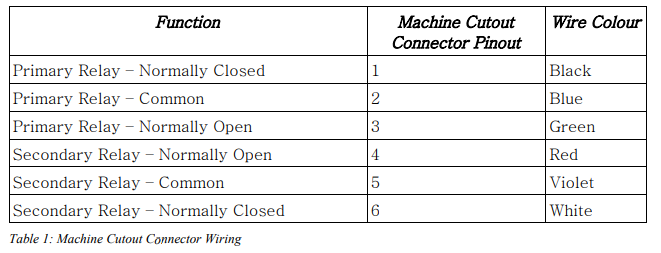
The wires on the machine cutout connector may need to be
extended
A typical LMI outputs a 12V signal to the machine ECU - which will then electronically
disable the boom functions (if this line is opened). Or the 12V line may be connected to a
solenoid. When the LMI wants to produce a cutout it opens the 12V supply line to the
solenoid. When the solenoid is closed, it prevents hydraulic oil flow for the boom lower and
extend functions. To utilize this cutout function, cut the line from the LMI to the ECU (or
solenoid). Join one side of the cutout line to the primary relay normally closed wire and the
other side of the line - to the primary relay common wire. When either the LMI or Gen3 LMS
wants to produce a cutout, they open the 12V supply line going to the ECU (or solenoid).
Single Cutout
Other LMI systems can have two cutout lines connected to two solenoids for each of the
boom down and boom extend functions. This can be connected in a similar fashion as the
single cutout line system by connecting the primary relay wires to one of the cutout lines as
above and then connect the other cutout line to the secondary relay wires. Both the primary and
secondary relays in the Gen3 LMS will be active at the same time.
Double Cutout
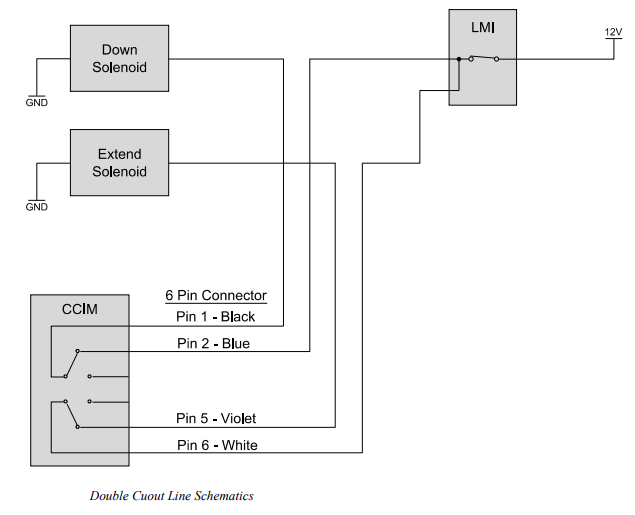
Some machine hydraulic controls have a boom movement disable function as a safety
feature; or as a road mode function to stop the operator inadvertently operating the boom
while moving. This will produce a full cutout - stopping all boom controls and can be used
for the cutout of the Gen3 LMS. Most machines have the hydraulic cutout function fail to safe, which means the output line
from the LMI to the solenoid is opened to produce a cutout. But some machines function in
the opposite manner. They apply a 12V power source to the solenoid line to produce a
cutout and they open the line to allow normal boom operation. This requires the Gen3 LMS
cutout to be connected in parallel with the existing LMI cutout line. Splice the normally
open wire from the primary relay into the cutout line and connect the common wire from
the primary relay to a constant 12V supply - preferably from the same power supply line for
the LMI (this way it is guaranteed to be able to supply enough current to a solenoid). The
same method can be used on the secondary relay if the LMI uses two cutout lines.
Parallel Cutout
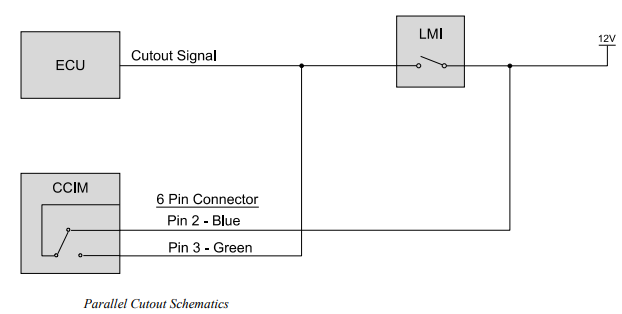
Some machine electronics have the LMI directly integrated into the machine and use
electrovalves to control the boom functions. An electrovalve is a proportional control that
opens the valve based on a Pulse Width Modulation (PWM) signal. The higher the duty
cycle of the PWM signal, the more the valve is open - allowing for more oil flow.
When the lines to the electrovalves for the boom lower and extend functions are opened,
an aggravated movement cutout is produced. Also when the lines are opened, the
machine ECU produces an open line fault error - indicating that the line was cut. This error
usually doesn't get cleared until the line is reconnected and the machine restarted. Usually, while this error is produced, all boom functionality and maybe even drive
functionality is disabled. To overcome this error (when a cutout is produced), the output to
the electrovalves needs to be redirected through a dummy resistor - so the desired
aggravated movement cutout is produced without creating a open line fault error. There
are four 4.7 Ohm and four 25 Ohm 25 watt resistors supplied with the kit. By combining
these two types of resistor values between 9 to 25 Ohms can be produced. The value of
the resistor to use will depend on the system, if the value is too high, the open line fault
error will again be produced. If the value is too low, too much current will be drawn through
the relays and wires - causing damage to the system. The system can be damaged by excessive current. To determine the resistor value, connect the 25 Ohm resistor to the input connector for one of the electrovalves and see if
the open line error is produced (make sure to move the boom in the direction that will attempt to energize the electrovalve with the maximum PWM signal). If the error is still
produced, connect another 25 Ohm resistor in parallel producing an effective overall resistance
of 12.5 Ohms and check if the open line error is produced, continue to lower the resistance
until the open line error is not produced.
Do not connect only one of the 4.7 Ohm resistor to the
electrovalve input, this will cause 36 watts of power
dissipation over the resistor which is only rated for 25 watts,
this will heat up the resistor and can start a fire.
Once the correct resistor value is determined, splice one side of the resistor into the power
input line (going into the electrovalve). Connect the other side of the resistor to the normally open
wire from the primary relay. Cut the ground input line into the electrovalve, join the side of
the ground input line that is connected to the electrovalve, to the normally closed wire from
the primary relay and join the other side of the ground input line to the common wire from
the primary relay. Repeat the same connections using the secondary relay wires for the
other electrovalve if required.
Electrovalve Cutout
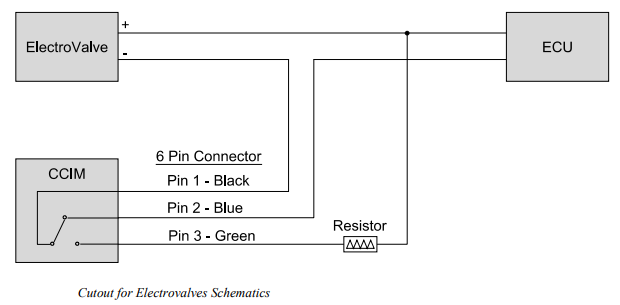
An auto electrician may be required to fit the cutout if the
electrovalve resistor method is used
Some of the older machines may not have a hydraulic cutout installed. However, since a
hydraulic cutout is now required by the standards, most of the machine manufacturers have
a retrofit hydraulic cutout kit available. Check with the machine manufacturer to see if they
have a hydraulic cutout kit available for your model. The Gen3 LMS cutout can be
connected into the hydraulic cutout kit using one of the methods above. If a retrofit hydraulic cutout kit is not available from the manufacturer then a cutout will
need to be installed. This will require installing solenoid check valves into the hydraulic
lines to either block or redirect the flow back to the tank for the boom down and boom
extend functions. The solenoid valves will require a high current power supply from the
machine electronics. Once the solenoid valves are installed and are sufficiently powered,
the Gen3 LMS cutout can be installed the same as shown in the Double Cutout
Line Schematics illustration.